GD&T - Composite Position
This Knowledge Base article describes how to configure and report Composite Position using CMM-Manager. For a detailed description of the Composite Position tolerance and how it is properly applied, refer to the appropriate topic in the current ASME 14.5 Dimensioning and Tolerancing publication, which is available from ASME website: https://www.asme.org/
Composite Position reports the positional tolerance of a pattern of features (taken as a whole) relative to a set of datum features, as well as reporting positional tolerance between the features in the pattern. There are two components to composite position tolerance:
• PLTZF - Pattern Locating Tolerance Zone Framework - this specifies the larger positional tolerance for the feature pattern; that is, the location of the pattern as a whole relative to a set of datum features.
• FRTZF - Feature Relating Tolerance Zone Framework - information that governs feature-to-feature relationships: the smaller positional tolerance for each feature within the pattern. Datum features specified for the FRTZF govern the relationship of the FRTZF to the PLTZF.
To report a Composite Position of a feature, click the Composite Position icon from Report => GD&T in the Ribbon Bar.
Enter the required information and parameters then select Preview or click OK to complete the operation.
Title (Optional - CMM-Manager 2022 or above):
- Enter text here to display items such as Balloon numbers or Key Characteristic numbers from the print in the report.
Reporting Features:
- Enter controlled features to be reported. To select, the user can either left-click features in the Display Window or drag- and-drop features from the Feature Database.
Note:
- Enter optional descriptive text to be displayed as a note in the report output.
PLTZF Zone:
- Type in the tolerance value specified in the PLTZF from the print.
- If a material modifier is called out for controlled features, you must output the size of all features before the composite position operation. MMC/LMC option will not be available otherwise.
FRIZF Zone:
- Type in the tolerance value specified in the FRIZF from the print.
- If a material modifier is called out for controlled features, you must output the size of all features before the composite position operation. MMC/LMC option will not be available otherwise.
Two Separate Feature Control Frames:
- When checked, the Two Separate Feature Control Frames checkbox indicates that the same geometric characteristic will be applied to both the PLTZF and the FRTZF. CMM-Manager will use the FRTZF datum features to report on the relationship of features within the pattern.
- i.e. Enable this option if there is 2 separate position symbols for upper and lower control frames.
- Clear the Two Separate Feature Control Frames checkbox to verify feature position relative to the datums, as well as relationship between the features.
- i.e. Disable this option is there is a single position symbol for upper and lower control frames.
PLTZF Features:
Specify the datum structure for the PLTZF here.
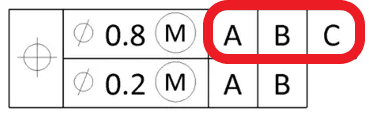
- Datum Ref Frame - When this option is selected, the current part reference frame is used for the position tolerance calculation.
- Please ensure that the current reference frame represents the datum structure specified in the print before reporting.
- Datum Feature #1, #2, and #3 are used to indicate primary, secondary, and tertiary datums on the report.
- If the material modifier is called out on datum features, you must output their sizes before this operation. The MMC/LMC options are unavailable otherwise.
- Defining datum features here is optional if no material condition exists (the current ref. frame is used for the calculation regardless).
- Datum Features - This allows the user to construct the temporary reference frame for the calculation.
- Datum Feature #1, #2, and #3 are used to indicate primary, secondary, and tertiary datums on the report.
- If the material modifier is called out on datum features, you must output their sizes before this operation. The MMC/LMC options are unavailable otherwise.
- Unlike Datum Ref Frame, defining datum features here is mandatory even if no material modifier is involved.
Datum Features option cannot accommodate all possible datum structures; therefore, please revert back to Datum Ref Frame if the error message is received when constructing a datum frame.FRTZF Features:
Specify the datum structure for the FRTZF here.
- Datum Plane - Select the datum plane for the FRTZF. Only plane feature is allowed.
- Datum Features - Select the datum feature for the FRTZF. Plane, cylinder, and line features are accepted.
Example #1:
Here is the typical composite position application... Hole pattern.
Assuming that your current reference frame represents the datum reference frame for PLTZF (ABC), the composite position settings required to output the report correctly is below. Please note that diameters of all 4 circles must be reported beforehand for the MMC options to be enabled.
Example #2:
Although less common, the composite position may appear when constraining coaxial series of holes.
Below is the correct report setting for this scenario.
Related Articles
Bilateral True Position of a Slot
Bilateral True Position (Slot actual parallel to slot nominal) This is how most people think of True Position. It is simply derived from the “offset” of the actual to the nominal. In our example here, we have a tolerance band of +/- 0.025 (TP ...
Reporting the T deviation of a point
When no CAD is available for reporting Cloud to CAD, in particular on manual CMM's, CMM-Manager offers a solution to report an actual point that was not measured in precisely the correct 3D location by projecting that point to a position directly ...
Free Position Alignment
A Free Position Alignment is used in a part program to create rough origin point from which your program can create a determinant reference frame using DCC commands without any further operator input. A Free Position Alignment can be created online ...
True Position of a Cylinder
True Position (Cylinder perpendicular to the axis system) This is how most people think of True Position. It is simply derived from the “offset” of the actual to the nominal. In our example here, we have a tolerance band of +/- 0.025 (TP tolerance of ...
Save Report Automatically for use with Discus
Once you've taught a program and create Report(s) it is possible to configure CMM-Manager program to automatically save report document in a format compatible with Discus CMM each time the program is run. Set Report Properties as follows: View the ...