Do you manufacture parts in distinct operations? Is the part also inspected after/during each of these distinct manufacturing operations? Are you creating unique CMM-Manager programs for each operation? If so, there is a better way
...Meet Operation Planner...
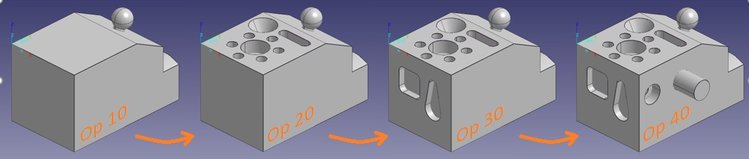
Operation Planner allows users to effectively create sub-programs from one main program. The main benefits include the speed at which the sub-program (Operation Plan) is created and the fact that only one program must be maintained. Imagine the amount of effort required for a Drawing Revision change; if you are using multiple programs, with Operation Planner, you just change the main program, and all Operations Plans automatically update.
- Create a complete inspection program in the usual manner. Think First Article or Last Article inspection here... Just create a program that inspects and reports all characteristics on drawing.
- Define the Operation Planner Safe Cube. This is a cube in which the probe will move outside in the case that measurement operations are skipped during Operation Plan execution - more on this later.
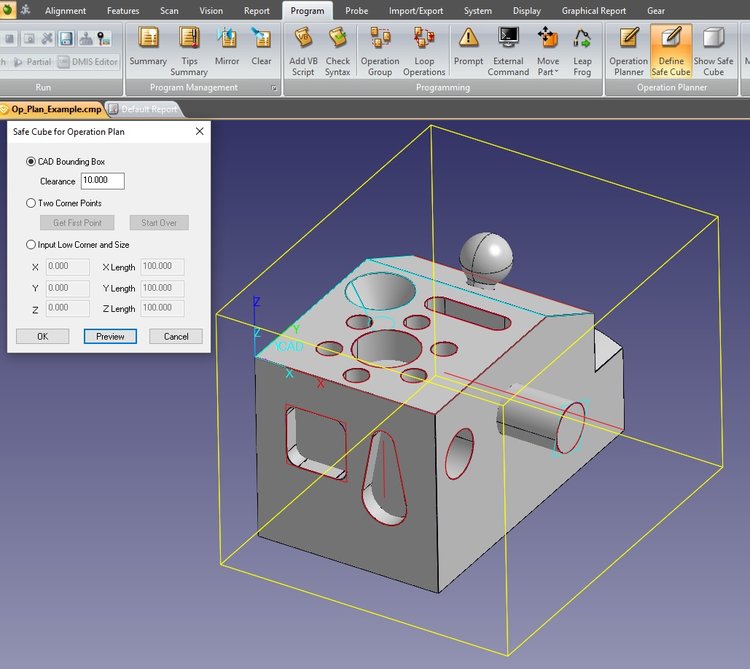
- Create Operation Plan by multi-selecting (use Shift or Ctrl keys) Operations from the Program Database, right-click, and choose Operation Plan. Important - Typically, you will choose the first few Operations in the Program, including the main Alignment. See examples for Op 10 and Op 20 below.
- Select Operations 1-17, right-click Operation Plan
- Select Operations 1-10 & 21-38, right click Operation Plan
Now you can run each Operation Plan by clicking the Operation Planner button from Ribbon Tab>Program>Operation Planner>Operation Planner. Select the Operation Plan you'd like to run and press the Run button.
Also, notice the "Keep original paths for consecutive measurement" check-box. When unchecked, each measurement operation will include a clearance move (before and after) outside the current Clearance Cube. Checking this box will allow originally planned paths to execute for consecutive program operations, thus maintaining a more efficient probe path. In general, the Clearance Cube is used when any portion of the original program is skipped, allowing safe program execution even when the tip angle is different from one block of the program to the next. The Operation Plan shown below shows that the Probe will move outside of the Clearance Cube as the program skips from Operation 10 to Operation 21.
Now you have one CMM-Manager program that allows running 5 different part configurations.
Complete Part - Run the program as usual
Op 10 - From Operation Plan, choose Op 10 and press the Run button
Op 20 - From Operation Plan, choose Op 20 and press the Run button
Op 30 - From Operation Plan, choose Op 30 and press the Run button
Op 40 - From Operation Plan, choose Op 40 and press the Run button
Related Articles
Adjusting Probe Path for Measured Feature
When creating or editing feature measurement paths on a DCC CMM, the user may need to adjust path due to obstacles in measuring environment such as clamps, vices, vee-blocks, etc. It is advised that the user take advantage of the tools provided in ...
zCat Portable CMM (DCC)
zCat Portable CMM Minimum Firmware: BOOT-02-06-18 (original release 3.7) Recommended Firmware: BOOT-06-01-18 (tested since 3.8 SP1) License Type: I++ / DME Required Software: Cat Smarts (included with hardware) I++ Server Type set as zCatServer - ...
Sheffield - SMP / UMP (DCC)
Models: SMP-300, SMP-350, SMP-400, UMP-360 Connection: Serial / RS-232 *null modem Default settings: 19200, O, 8, 1 (SMP-300/350) 57600, O, 8, 1 (SMP-400) Scanning machines with SMP-400 can communicate at either 57600 or 115200 SP25 Instructions to ...
DEA-Tutor-P (DCC)
Tutor-P Default settings: 9600, E, 8, 1 Required Files: Cosdat Binary File - Cosdat1.bin Other Files: Error Comp File - Comp.dat / comp.asc
I++ / DME (DCC)
See this post - Renishaw UCC I++ Install Guide - for Renishaw UCC I++ systems.