When creating or editing feature measurement paths on a DCC CMM, the user may need to adjust path due to obstacles in measuring environment such as clamps, vices, vee-blocks, etc. It is advised that the user take advantage of the tools provided in the Measurement Tab first before resorting to manual adjustments available in the Points or Path Tab of the Measurement Dialog. Any adjustments performed from either Points or Path Tab will result in some form of a "Locked" Path. meaning, upon re-editing this feature the user must first uncheck the Lock Path checkbox in order to access the Tools to manipulate Points or Path entities.
Considering a part and clamps as shown here:
There are several scenarios for adjusting path(s) to avoid clamps.
- When programming with 3D CAD, it's possible to edit as mentioned below and also by manipulating the CAD directly, using tools in the Measurement Tab, or by editing the Points Tab.
- When programming with no CAD, there is really only one option. The user must add Move Points either when Teaching by Joystick or edit previously created path from the Path Tab.
We'll cover each scenario below, listing the optimal methods first.
1. Import or Edit the CAD Directly - It may seem like extra steps but having CAD for these obstacles will pay off in the end. This method works best with Automatic Path Planning, not only does the path for newly created feature automatically avoid the obstacle but also paths that are adjusted after moving the feature operation in the program. Yes, the path will automatically update by simply dragging the Feature from one location in program to another.

It's possible to create your own CAD elements by simply joystick / manually measuring the obstacle as simplified geometry.
For example, you can measure just a small cylinder and plane that roughly represent the boundary of the obstacle, then Right-Click the feature(s) from Feature Database and choose Add to CAD...
2. Tools from Measurement Tab - Many times it is possible to adjust the desired path using tools provided on the Measurement Tab. As before, this method works well with Path Planning, allowing user to move features within program, re-Create Path, etc. all without the barrier of the "Locked" Path. In the example below, the Range Adjust button was used to reduce the length of the line, thus avoiding the finger clamp. The tools available in the Measurement Tab vary from one feature type to another, for example a Cone and Cylinder have depth as well as radial options in the Range Adjust interface.
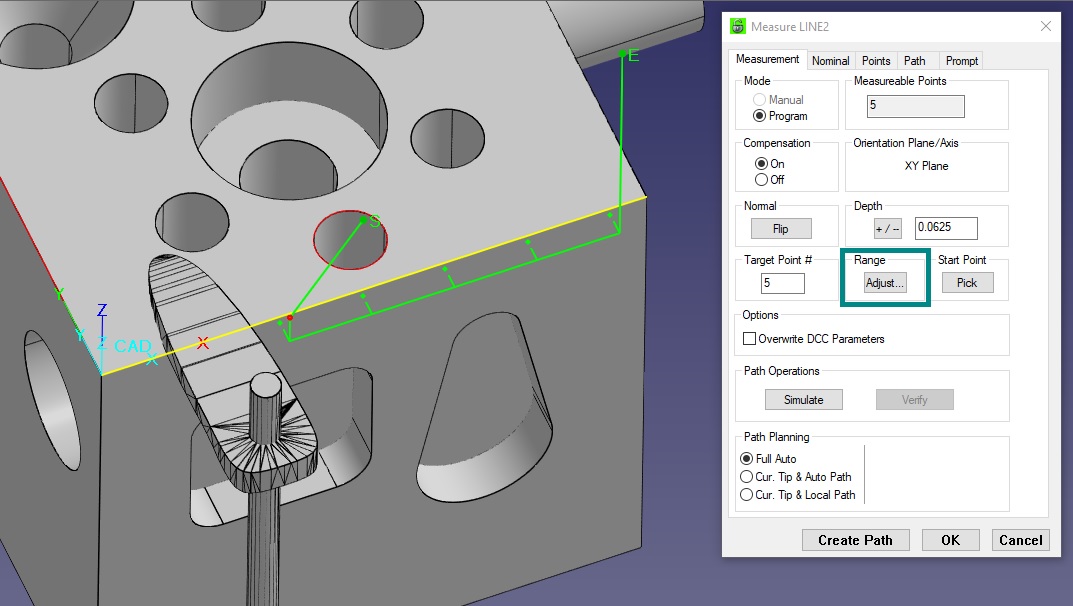
3. Adjustments from Points Tab - Sometimes no amount of adjusting from the Measurement Tab will do. In this case, we've removed one point by selecting the desired point and clicking the "Delete Select" button. It is also possible to adjust points by keying in values or dragging graphically, adding points by Picking from CAD, etc. As with the previous two methods, this works well with Path Planning as the link paths are recalculated automatically when dragging within program or adding new nearby features.
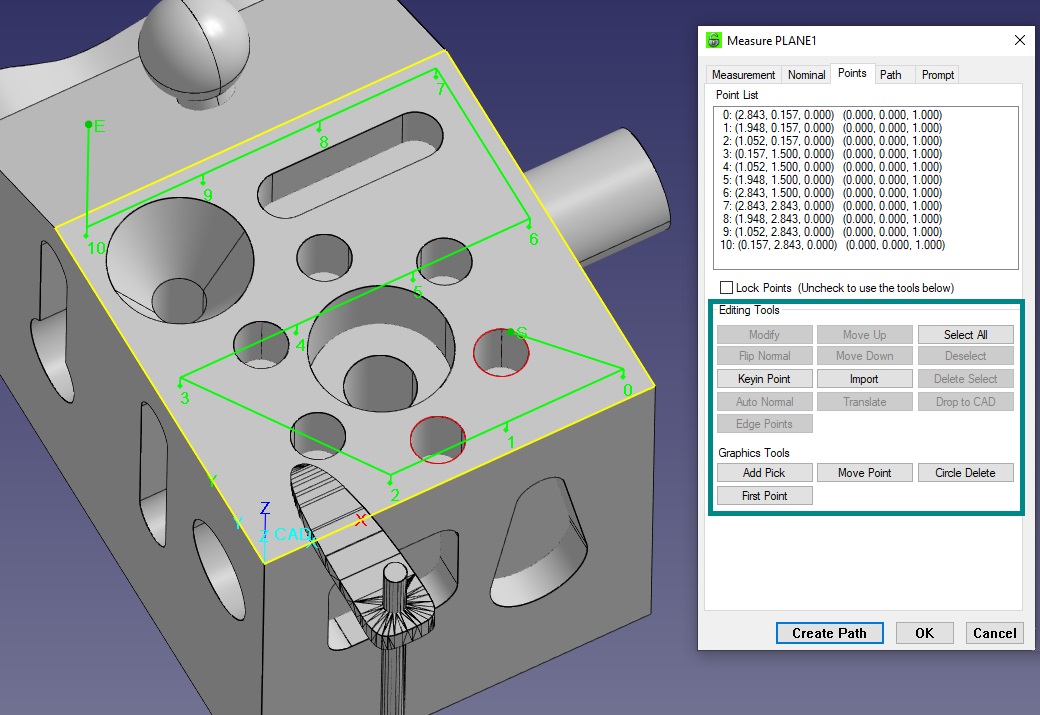
3. Adjustments from Path Tab - While programming by Define Teach or Joystick Teach, it is common to use this method to add or adjust Probe Path. It is not recommended to use this method when programming from CAD as the benefits of Auto Path Planning diminish due to "Locked Path" after adjustments are made. In this case the "Locked Path" will prevent user from re-Creating Path in any way, extra mouse clicks are needed to unlock path, then any changes made will be undone when pressing Create Path on the Measurement Tab. This method should only be used as a last resort for path adjustment. If using this method, we suggest that you wait until the entire program is complete, thus allowing easy program sorting and editing before editing and Locking these individual paths.
Related Articles
Adding CAD Furniture
What is Furniture? The furniture feature allows a user to define fixed models in the workspace that the system will consider when planning paths to avoid collisions. These furniture pieces will remain at their defined location and orientation when ...
Path Creation Preferences
Unlike tradition path planning that uses Clearance Planes, Cubes, etc., CMM-Manager creates feature paths automatically when 3D CAD is available. After specifying minimal parameters or simply using the default parameters, CMM-Manager is able to ...
Programming with Part and Fixture CAD Models
The main advantage of utilizing the fixture CAD file in conjunction with the part model is that CMM-Manager will generate a measurement path to avoid both details, eliminating any manual adjustments. For example, programming the part shown in the ...
Operation Planner Tutorial
Do you manufacture parts in distinct operations? Is the part also inspected after/during each of these distinct manufacturing operations? Are you creating unique CMM-Manager programs for each operation? If so, there is a better way ...Meet Operation ...
How To - Calibrating Probe Head
In the event of a probe crash, the probe head may become misaligned, causing unintended probing errors. One way to quickly isolate and determine if this is the issue involves: Selecting the A0B0 reference tip Clear the tip calibration by: Updating ...